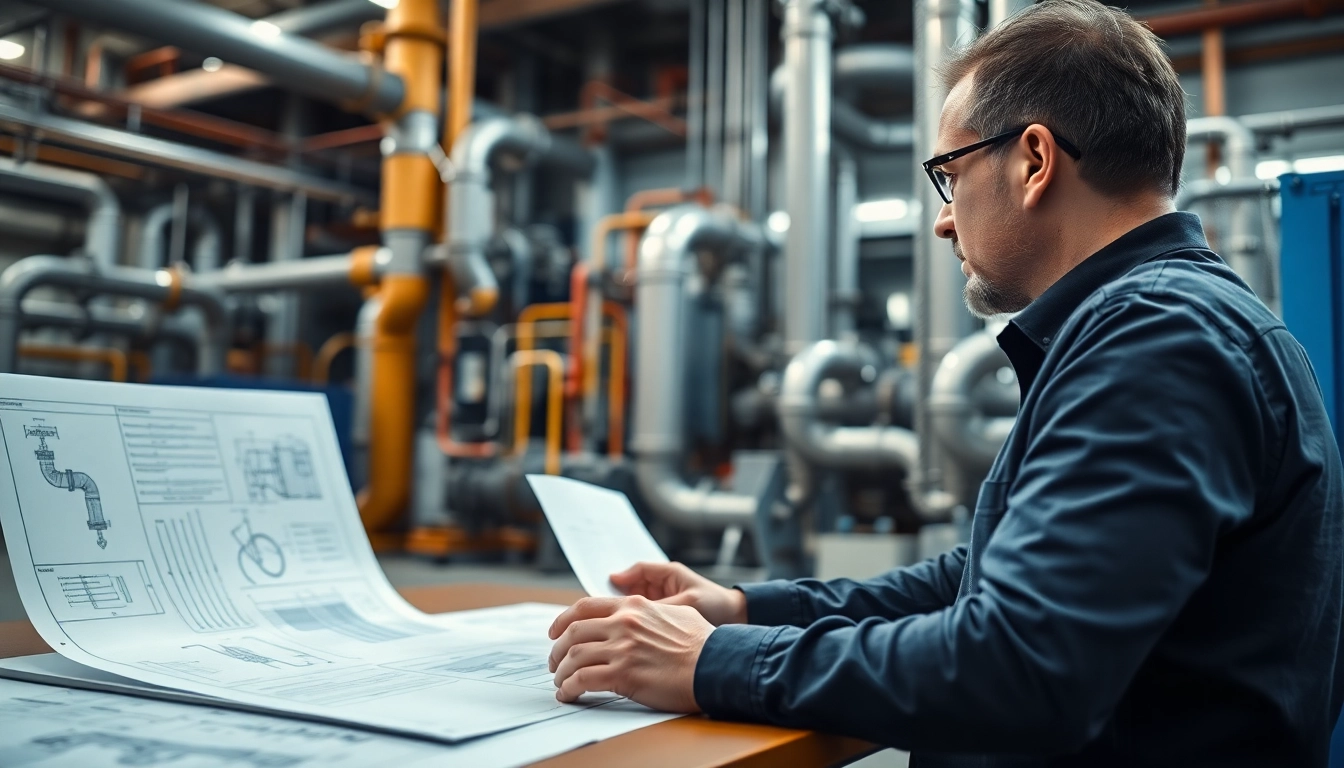
Understanding Pipe Stress Analysis
Pipe stress analysis is a crucial aspect of engineering, particularly in industries dealing with complex piping systems such as oil and gas, power generation, and chemical processing. It involves evaluating the stresses, displacements, and loads acted upon a piping system due to various factors like internal pressure, temperature changes, and external forces. This assessment is essential for ensuring safety, integrity, and efficiency in piping designs. By understanding pipe stress analysis, engineers can develop systems that withstand operational challenges and minimize risks.
What is Pipe Stress Analysis?
Pipe stress analysis is an engineering process that helps determine how physical forces affect piping systems under specific conditions. This analysis considers various factors such as:
- Internal Pressure: The pressure within the pipe can induce stress, particularly in areas with bends or fittings.
- Thermal Expansion: Changes in temperature cause pipes to expand or contract, leading to thermal stress.
- Weight: The weight of the piping, fluids, and insulation must be accounted for.
- External Forces: Environmental factors such as wind, seismic activity, or changes in ground conditions can add stress to the system.
Engineers utilize various methodologies, including software tools and manual calculations, to assess these stresses and determine the system’s ability to maintain integrity under load.
Importance of Pipe Stress Analysis in Engineering
The importance of pipe stress analysis cannot be overstated. Here are several key reasons why this analysis is vital in engineering:
- Safety: Ensuring that the piping system can withstand the operational pressures and temperature fluctuations reduces the risk of failures and accidents, thus protecting personnel and the environment.
- Cost Efficiency: By identifying potential failures before they occur, companies can avoid expensive repairs and downtime, which enhances overall operational efficiency.
- Compliance: Many industries are subject to stringent regulatory standards; proper stress analysis ensures compliance with safety codes and regulations.
- Design Optimization: The analysis enables engineers to refine designs to be as cost-effective while maintaining reliability, resulting in more robust systems.
Common Applications of Pipe Stress Analysis
Pipe stress analysis is applicable across various industries, including:
- Oil and Gas: Analyzing pipelines that transport crude oil or natural gas to withstand the high pressures involved.
- Power Generation: Assessing cooling water and steam pipes to ensure their stability during temperature shifts.
- Chemical Processing: Evaluating complex piping systems in chemical plants where various materials react under different pressures and temperatures.
- Construction: Ensuring that newly constructed systems meet structural integrity requirements.
Fundamentals of Pipe Stress Analysis
Key Concepts in Pipe Stress Analysis
Understanding pipe stress analysis involves several key concepts, including:
- Primary Stresses: These are permanent and arise from normal operational loads such as pressure and temperature. Primary stresses must be evaluated per industry standards like ASME B31.3.
- Secondary Stresses: These are reversible and occur due to thermal expansion and contraction. They also include stresses that develop from deflection.
- Occasional Loads: These include loads that are not typically present during normal operation but may occur during specific circumstances, such as seismic events or extreme weather conditions.
Types of Stresses Encountered
The primary types of stresses encountered in piping systems can be categorized as follows:
1. Bending Stress
Occurs when a pipe is subjected to forces that cause it to bend, which can happen at joints and supports.
2. Axial Stress
Resulting from internal pressure and temperatures that create elongation or contraction in the pipe length.
3. Shear Stress
Develops along surfaces that are subjected to forces parallel to the surface — often encountered at supports and connections.
Materials and Their Impact on Analysis
The materials used in pipe construction significantly affect the stress analysis. Common materials include:
- Carbon Steel: Known for its strength and cost-effectiveness, commonly used in oil and gas pipelines.
- Stainless Steel: Offers up resistance to corrosion, suitable for chemical and food industries.
- Plastic: Used in low-pressure systems, often in residential water lines.
Different materials exhibit distinct stresses under loads, and understanding these characteristics is essential for conducting an accurate analysis.
Methods of Conducting Pipe Stress Analysis
Software Tools for Pipe Stress Analysis
Various software applications are available to assist engineers in pipe stress analysis. These tools allow for complex simulation and analysis, such as:
- CAESAR II: A widely-used tool that performs static and dynamic stress analysis on piping systems.
- ANSYS: Offers finite element analysis (FEA) capabilities, giving insights into stress distribution across piping systems.
- AutoPIPE: Provides integrated modeling and stress analysis, particularly beneficial for large projects.
Manual Calculation Techniques
While software tools are essential, manual calculations remain relevant for smaller projects or educational purposes. Common methods include:
- Using formulae based on material properties and external load conditions to calculate stresses.
- Applying beam theory to analyze simple spans or complex arrangements of connectors and supports.
Best Practices for Accurate Analysis
To ensure accuracy in pipe stress analysis, the following best practices should be adhered to:
- Regularly calibrate software tools based on up-to-date engineering standards.
- Engage in thorough review sessions with cross-discipline teams to capture all potential stress points.
- Keep detailed records of calculations and decisions made during the analysis for future reference and validation.
Case Studies: Successful Pipe Stress Analysis
Real-World Examples of Pipe Stress Analysis Application
Several case studies illustrate the successful application of pipe stress analysis:
- Oil Platform Design: A major oil company faced catastrophic failures in piping systems due to inadequate stress analysis. After employing detailed analysis using CAESAR II, they redesigned critical sections, leading to enhanced system reliability.
- Chemical Plant Upgrade: A facility was upgraded with new piping that underwent thorough stress analysis to accommodate high-pressure operations. By analyzing thermal expansion issues, engineers successfully prevented pipe ruptures.
Lessons Learned from Industry Cases
From these case studies, several lessons emerge:
- Investing in quality analysis tools can yield significant long-term savings.
- Regular updates and reviews of piping systems can preempt failures and security breaches.
- A multidisciplinary approach can uncover overlooked stress points that may lead to failures.
Impact on Project Safety and Integrity
Successful pipe stress analysis fundamentally enhances project safety and integrity. It reduces the potential for accidents, ensuring compliance with safety regulations and contributing to a culture of safety within engineering practices.
Future Trends in Pipe Stress Analysis
Technological Advancements in Pipe Analysis
As technology evolves, so does the ability to conduct more thorough analyses. The future will likely see:
- Increased Use of AI: Automated analysis and prediction of potential failures using machine learning algorithms.
- Real-time Monitoring: Integration of IoT devices for live readings and stress tracking during operations.
The Role of AI and Automation
AI’s infusion into engineering enhances predictive analysis capabilities, allowing systems to adapt pre-emptively to stress changes. Automated inspections combined with databases of historical failures offer insights that drastically improve design accuracy.
Preparing for Changes in Industry Standards
With the evolving nature of engineering standards, organizations must stay abreast of changes in regulatory guidelines regarding piping systems. Continuous training for engineering personnel in new methodologies and practices will be vital to the longevity and safety of industrial projects.