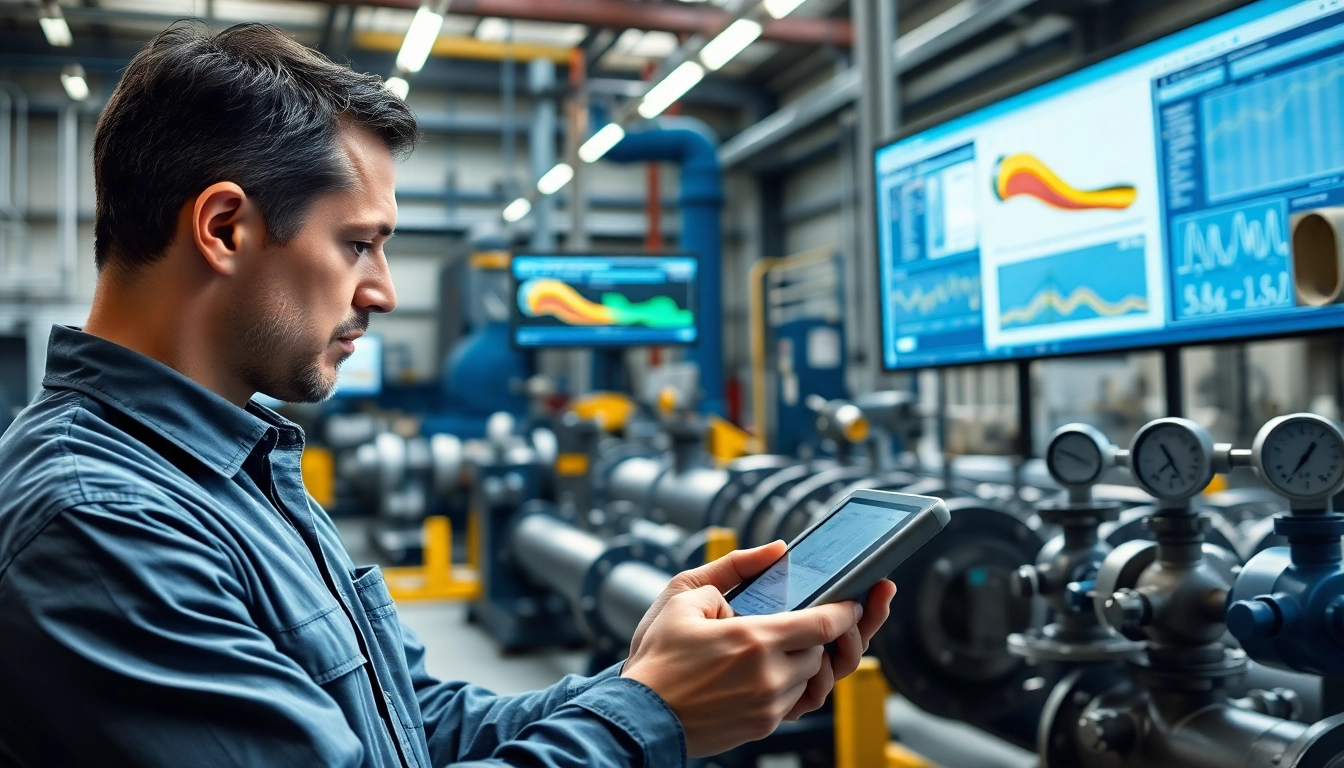
Understanding Pipe Stress Analysis
What is Pipe Stress Analysis?
Pipe stress analysis is a critical engineering process that evaluates the mechanical behavior of piping systems under various conditions. Specifically, it examines how pipes react to loads, including thermal expansion, weight, seismic events, and pressure. As piping systems are integral to many industries including oil and gas, power generation, and chemical processing, understanding their stress responses is essential for safety and efficiency.
Through this analysis, engineers can determine whether a pipe can withstand anticipated forces and moments without failing. The scope of analysis incorporates different factors, such as material types, operating temperatures, and environmental conditions, ensuring that each system is designed to endure its operational demands.
Importance of Pipe Stress Analysis in Engineering
The significance of pipe stress analysis in engineering cannot be overstated. It serves several vital functions:
- Ensuring Safety: Engineers rely on stress analysis to prevent failures that could lead to catastrophic accidents, including leaks and ruptures.
- Regulatory Compliance: Many industries are required to adhere to strict standards and guidelines; thorough stress analysis helps assure compliance with safety regulations.
- Cost Efficiency: Proper analysis can significantly reduce the risk of failures, which not only mitigates potential legal costs but also avoids costly downtime and repairs.
- System Efficiency: It helps engineers optimize design to manage loads effectively, enhancing operational efficiency throughout the life cycle of the piping system.
Common Applications of Pipe Stress Analysis
Pipe stress analysis finds applications across various sectors, including:
- Oil and Gas: Ensuring the integrity of pipelines transporting hydrocarbons under high pressure and fluctuating temperatures.
- Power Plants: Analyzing the distribution of thermal stresses in systems that handle steam, water, and other fluids.
- Chemical Processing: Assessing the strength and stability of pipes carrying corrosive substances.
- Water Treatment Facilities: Evaluating the stresses involved in managing heavy pipeline systems.
Key Principles of Pipe Stress Analysis
Fundamental Concepts in Stress Analysis
At the core of pipe stress analysis are fundamental concepts that engineers must grasp. Stress is defined as the internal resistance of a material to deformation; it can be categorized into:
- Tensile Stress: Occurs when forces attempt to elongate the material.
- Compressive Stress: Happens when forces push the material closer together.
- Bending Stress: Arises from external moments that cause the material to bend.
Understanding these stresses allows engineers to determine appropriate material selection and design parameters to mitigate failure risks.
Materials and Their Behavior Under Stress
Different materials behave differently when subjected to stress. Key material considerations include:
- Metals: Known for their tensile strength, ductility, and fatigue resistance. Steel, for instance, is commonly used for its durability and ability to withstand high pressures.
- Plastics: While lighter and corrosion-resistant, plastics can be less durable under high temperatures or stress.
- Composites: These materials combine properties from different elements, offering tailored solutions in specific applications but necessitating careful analysis of joint strengths.
By understanding material properties, engineers can avert material failure, particularly in high-stress environments.
Understanding Load Types and Their Effects
Load types are an essential factor in pipe stress analysis, impacting how pipes are supposed to behave. The primary loads include:
- Static Loads: These are loads applied gradually and held constant, such as the weight of the pipe and the media it carries.
- Dynamic Loads: These loads involve time-dependent effects, such as those experienced during earthquakes or rapid changes in pressure.
- Thermal Loads: Resulting from temperature variations which can cause expansion or contraction of pipes, elevating stress levels.
Cognizance of these loads and their interactions is crucial for ensuring a pipe’s integrity and longevity.
Tools and Software for Pipe Stress Analysis
Popular Software Solutions for Engineers
In modern engineering, several software packages are designed specifically for pipe stress analysis, enhancing the accuracy and efficiency of evaluations. A few notable software solutions include:
- CAESAR II: A widely used tool that simplifies stress analysis for piping systems and is compliant with various industry codes.
- AutoPIPE: Known for its user-friendly interface and integration capabilities, enabling comprehensive modeling for fluid dynamics.
- ANSYS: Provides powerful finite element analysis (FEA) capabilities, allowing for complex structural evaluations.
Comparative Analysis of Software Tools
When selecting a software tool for pipe stress analysis, it is essential to consider several factors:
- Compatibility: Ensure the software is compatible with existing systems and models.
- Ease of Use: User-friendly software can significantly reduce training time and enable engineers to focus on analysis rather than navigating complicated interfaces.
- Features: Robust feature sets such as 3D modeling, code compliance checks, and reporting capabilities enhance analysis depth.
- Support and Training: Reliable customer support and the availability of training resources are crucial for effective utilization of the software.
How to Choose the Right Tool for Your Needs
Choosing the right tool for pipe stress analysis should involve a comprehensive evaluation process:
- Define specific requirements based on project demands.
- Conduct a cost-benefit analysis to determine the overall investment versus the benefits provided.
- Request demonstrations and trials from software vendors to evaluate usability and features firsthand.
- Gather feedback from other users to understand their experiences and challenges with the software.
Best Practices in Conducting Pipe Stress Analysis
Implementing Effective Stress Analysis Strategies
To ensure thorough and effective pipe stress analysis, engineers should consider integrating several best practices:
- Baseline Assessment: Start with a comprehensive assessment of existing conditions and load scenarios.
- Multidisciplinary Collaboration: Engage experts from various disciplines—including materials science and fluid dynamics—to improve the analysis scope.
- Validation of Models: Utilize benchmarking and validation against historical data to ensure model accuracy.
Common Challenges and Solutions
Pipe stress analysis comes with its set of challenges, including:
- Data Accuracy: Ensuring that all data inputs, from material specifications to load conditions, are accurate can be a challenge. Implementing robust quality control measures can help.
- Complexity of Systems: As systems become more complex, analyses can become unwieldy. Employ model simplification strategies where appropriate to manage complexity without sacrificing accuracy.
- Regulatory Compliance: Staying on top of ever-changing regulations requires continuous education and adapting to industry standards.
Case Studies: Successful Pipe Stress Analysis Projects
Examining real-world examples of successful pipe stress analysis projects helps illustrate the practical value of these methodologies:
- Oil Refinery Expansion: A major refinery faced challenges in expanding their piping systems. Through detailed stress analysis, engineers could confidently design new additions that integrated seamlessly with existing infrastructure, increasing capacity without compromising safety.
- Nuclear Power Plant Upgrade: During upgrades to a nuclear facility, thorough pipe stress analysis was crucial for ensuring that aging pipes met new safety standards. The analysis revealed necessary reinforcements, ensuring continued operation while adhering to regulatory requirements.
Evaluating the Impact of Pipe Stress Analysis on Safety and Efficiency
Metrics for Measuring Success in Analyses
To evaluate the effectiveness of pipe stress analysis, engineers should employ various metrics:
- Failure Rates: Monitoring the rates of pipe failures before and after implementing stress analysis protocols can indicate the effectiveness of the approach.
- Compliance Incidents: Tracking compliance incidents related to code violations or safety breaches provides insight into operational integrity.
- Operational Downtime: Reduced downtime due to fewer pipe failures signifies the effectiveness of thorough analyses and proactive maintenance.
Long-term Benefits of Proper Stress Analysis
The long-term benefits of engaging in comprehensive pipe stress analysis are multifaceted:
- Enhanced Safety: Safety systems that are verified through stress analysis contribute to fewer accidents and incidents.
- Cost Savings: Reduced maintenance costs over time due to early identification of potential issues can lead to significant savings.
- Lifespan Extension: An optimized design based on stress analysis helps extend the lifespan of critical pipeline infrastructure.
Future Trends in Pipe Stress Analysis and Engineering
Looking ahead, several trends are emerging in pipe stress analysis:
- Increased Automation: The future is leaning towards automated analysis processes, minimizing human error and improving efficiency.
- Integration with IoT: The Internet of Things (IoT) will enable continuous monitoring of pipe stress in real-time, providing data that can prompt immediate action if necessary.
- Advanced Materials: Ongoing research into new materials and composites is likely to influence future practices in pipe stress analysis.