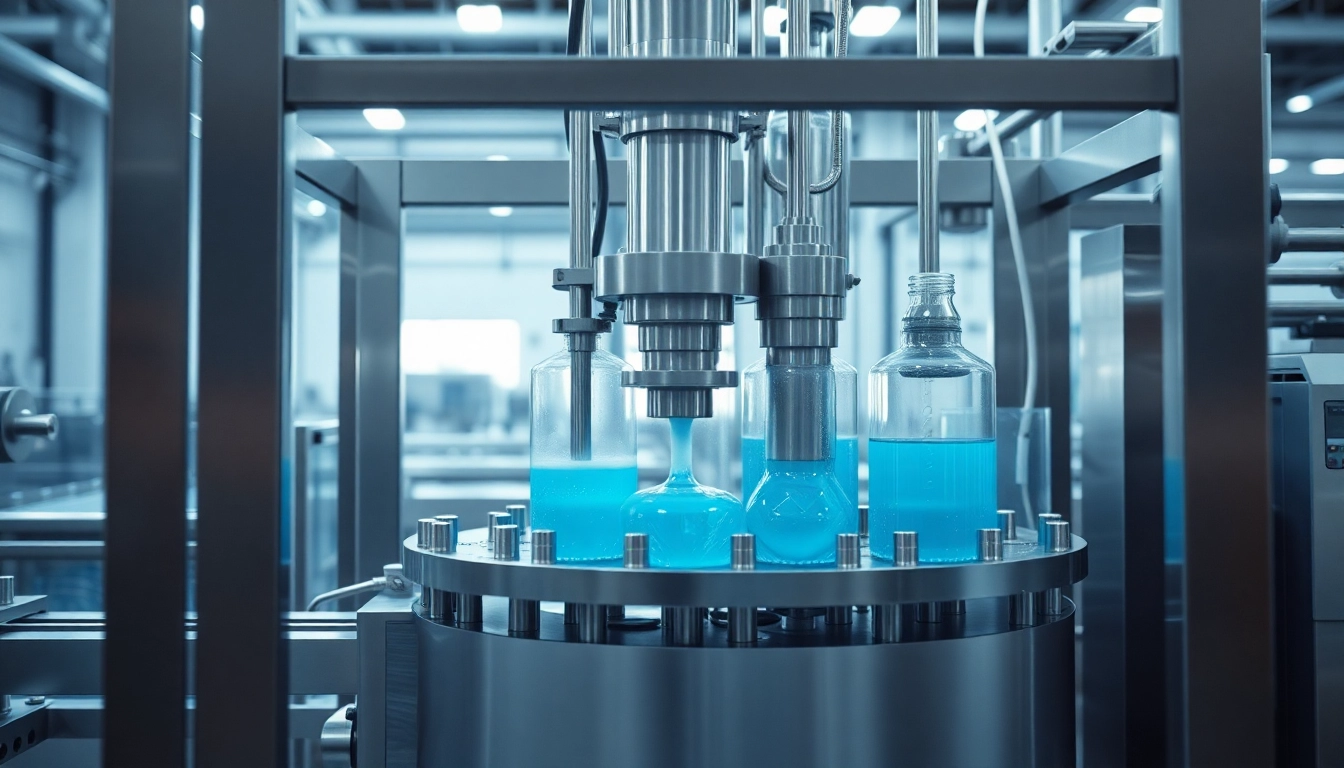
Understanding Liquid Packaging Solutions
Liquid packaging is a critical aspect of modern manufacturing and distribution, particularly for industries like food and beverage, pharmaceuticals, and chemicals. The process requires a precise balance between safeguarding product integrity and ensuring efficiency in packaging. As businesses increasingly turn to automation and innovative technologies, the role of a reliable Liquid Packaging Machine Supplier becomes paramount to success. In this article, we will explore the nuances of liquid packaging, focusing on the core elements, benefits, and types of machines available in the market.
What is Liquid Packaging?
Liquid packaging refers to the method of enclosing liquid products—ranging from beverages to industrial chemicals—in a manner that maintains their quality and facilitates easy distribution. This packaging process can vary significantly based on the type of product and its intended market. Common liquid packaging formats include bottles, cartons, pouches, and bags, each designed to accommodate specific liquids, such as water, sauces, or pharmaceuticals.
Key Benefits of Using Liquid Packaging Machines
Investing in liquid packaging machines provides numerous advantages for manufacturers:
- Efficiency: Automated machines significantly reduce the time required for packaging, allowing for high output rates that meet market demands.
- Precision: These machines ensure consistent filling levels and reduce waste, contributing to lower operational costs.
- Product Safety: Advanced packaging technology minimizes contamination risks, prolonging the shelf life of liquids.
- Customization: Manufacturers can design packaging that resonates with branding strategies, enhancing customer appeal.
- Regulatory Compliance: Automated systems aid in maintaining adherence to safety and quality regulations necessary in various industries.
Different Types of Liquid Packaging Machines Available
Various liquid packaging machines cater to distinct requirements, each equipped with unique functionalities:
- Fillers: These machines are designed to fill containers with liquids, including automatic, semi-automatic, and manual types. They come in various configurations—gravity fillers, pressure fillers, and vacuum fillers—each suited for different liquid viscosities.
- Cappers: Capping machines secure bottle closures and can apply caps of different types; this includes snap-on, screw-on, or cork caps.
- Labelers: They automatically affix labels to containers post-filling and capping, ensuring accurate branding and regulatory compliance.
- Palettizers: These machines organize and stack packaged goods onto pallets for easier transportation.
- Complete Packaging Lines: Integrated systems that combine filling, capping, and labeling in one streamlined process.
Choosing the Right Liquid Packaging Machine Supplier
Selecting the right supplier for liquid packaging machines is a crucial decision that can impact productivity and overall success. Here, we delve into the crucial elements to consider in this selection process.
Factors to Consider When Selecting a Supplier
When choosing a liquid packaging machine supplier, it is important to evaluate:
- Industry Experience: Suppliers with extensive experience in liquid packaging understand the unique challenges and can provide tailored solutions.
- Product Range: A diverse portfolio means that the supplier can cater to various needs, allowing you to choose machines that best fit different product lines.
- Customization Options: The ability to customize machines to fit specific requirements can enhance operational efficiency.
- Customer Support: Ongoing technical support and maintenance options are essential to minimizing downtime.
- Reputation: Research supplier reviews and testimonials to gauge their reliability and quality of service.
The Importance of Quality and Reliability
Quality should never be compromised when selecting a liquid packaging machine supplier. Reliable machinery minimizes operational hiccups and enhances productivity, directly impacting profitability. Opting for machines with robust build quality ensures longevity and reduces the need for frequent replacements or repairs.
How to Evaluate Supplier Credentials
To qualify a supplier’s credentials, consider the following approaches:
- Certifications: Ensure the supplier has necessary industry certifications that validate their machinery quality and safety standards.
- Case Studies: Request case studies or testimonials from other businesses to understand how the supplier has aided in operational improvements.
- Site Visits: If possible, visiting the supplier’s manufacturing facility can provide insights into their operational capabilities and machine quality.
- Trial Runs: Some suppliers offer trial runs for their machines, allowing prospective customers to see performance before purchase.
Innovative Technologies in Liquid Packaging
The liquid packaging industry is witnessing rapid innovations driven by technological advancements, enhancing efficiency and sustainability.
Automation in Liquid Packaging Machines
Automation stands at the forefront of modern liquid packaging solutions, enabling manufacturers to achieve precise filling, capping, and labeling with less manual intervention. Automated systems increase production speed, reduce operational costs, and minimize human error. Technologies such as robotics, AI, and IoT enable these machines to become smarter, capable of adjusting parameters in real-time based on production needs, thus optimizing workflows.
Eco-Friendly Packaging Solutions
In response to growing environmental concerns, many suppliers are now focusing on eco-friendly packaging technologies. These include:
- Biodgradable Materials: Use of bio-based or compostable materials that reduce plastic waste.
- Minimalist Design: Packaging solutions that use less material without compromising performance.
- Recycling Programs: Systems that promote recycling and use of recycled materials in packaging.
Future Trends in Liquid Packaging Technologies
As industries evolve, so do the technologies that support them. Key trends to watch in liquid packaging include:
- Smart Packaging: Integration of sensors and QR codes to provide real-time data on product freshness and quality.
- Higher Customization: Advanced printing technologies allowing brands to implement tailored packaging solutions for targeted marketing.
- Sustainability Integration: Ongoing development in materials that ensure packaging sustainability while meeting consumer demands.
Case Studies: Success Stories with Liquid Packaging Machines
Real-world applications provide a clearer picture of how liquid packaging machines contribute to business success. Here, we examine various industries carrying out successful implementations.
Food Industry Innovations
In the food industry, innovative liquid packaging machines have transformed how products are packaged. For instance, a well-known juice manufacturer integrated an automated packaging line that reduced labor costs by 40%, maintained higher hygiene standards, and improved packaging speeds, adapting to fluctuating consumer demands with ease.
Pharmaceutical Applications
For pharmaceutical companies, ensuring product safety and compliance with regulations is vital. A pharmaceutical firm deployed a state-of-the-art liquid filling system that provided accurate dosages while maintaining sterility, subsequently witnessing a 30% increase in productivity and a decrease in compliance-related incidents.
Chemical Packaging Solutions
The chemical industry often deals with hazardous materials, making reliable packaging crucial. A chemical manufacturer switched to automated packaging solutions, enhancing safety by minimizing manual handling, implementing robust containment systems, and significantly cutting down on accidents and material losses during the packaging process.
Maintaining Your Liquid Packaging Equipment
Regular maintenance of liquid packaging machines is vital to ensure longevity and optimal performance. Establishing a comprehensive maintenance routine can prevent costly breakdowns and downtime.
Routine Maintenance Best Practices
To maintain your liquid packaging equipment effectively, consider these best practices:
- Scheduled Inspections: Conduct regular inspections and service checks based on the manufacturer’s recommendations.
- Component Checks: Monitor wear and tear on critical components like pumps, valves, and seals, ensuring timely replacements.
- Calibration: Regularly calibrate machines to ensure precise fillings and various operational settings.
Common Issues and Troubleshooting
Common operational issues may arise, including:
- Inconsistent Fill Levels: Adjusting calibration settings or maintaining the feed system can often address these discrepancies.
- Mechanical Failures: Check for blockages, lubrication, and alignment issues regularly to prevent breakdowns.
- Label Misalignment: Ensure the label application system is correctly calibrated and clean to avoid misalignment and residue build-up.
Upgrades and Modernization Options
As technology evolves, consider upgrading to newer models or retrofitting existing machines with modern components. This may include integrating software for better monitoring and efficiency, adopting new filling technologies, or adding RFID systems to enhance inventory management.