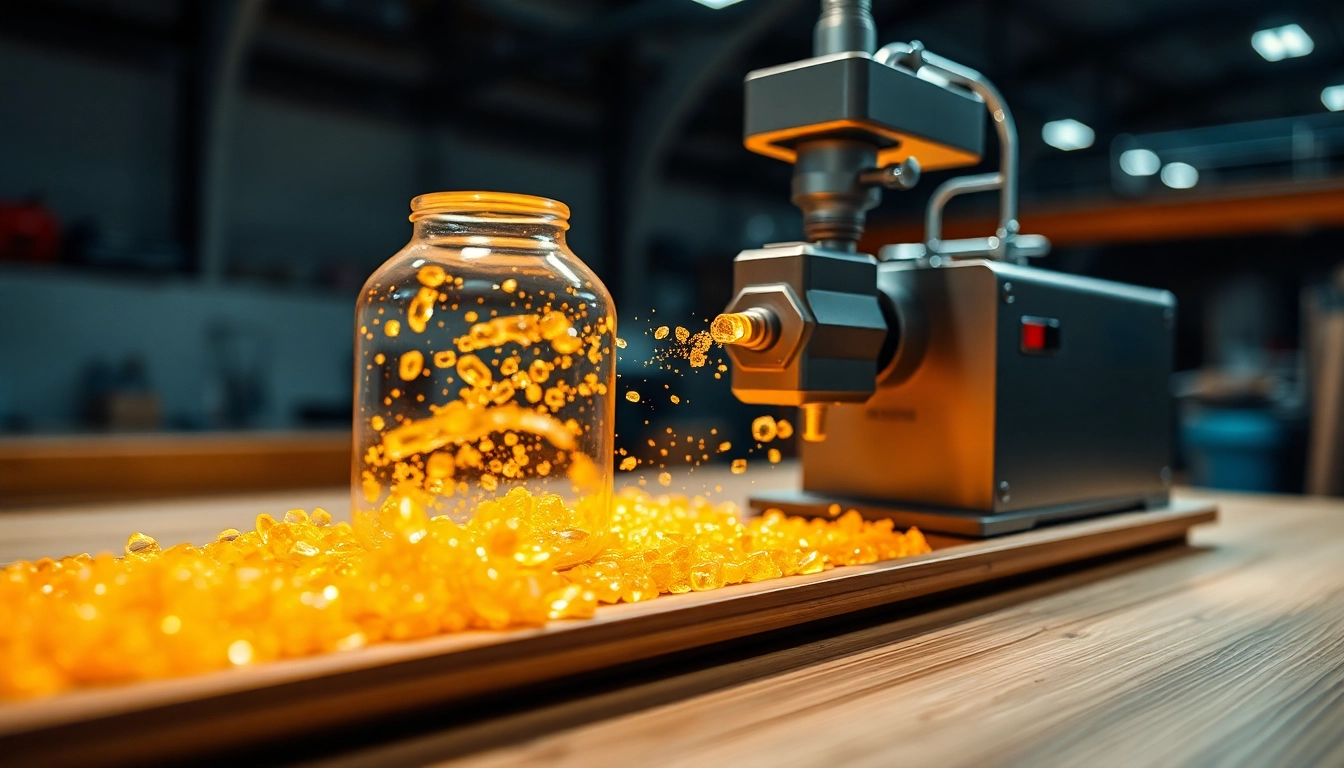
In today’s fast-paced industrial environment, the need for efficient packaging solutions has never been more critical. As industries expand and consumer demand for products increases, companies are turning to technology for streamlined processes. One essential technology enabling optimal packaging efficiency is the Liquid Packaging Machine Supplier. These suppliers provide diverse machine types designed for various liquid products, catering to multiple industries.
Understanding Liquid Packaging Machines
What is a Liquid Packaging Machine?
A liquid packaging machine is intended for packaging various liquid products, including beverages, chemicals, and pharmaceuticals. These machines can fill and seal containers automatically or manually, using several technologies to optimize speed, precision, and efficiency. The functionality typically includes filling, capping, and labeling, allowing for a complete packaging solution in one cohesive process.
Key Features and Benefits
Liquid packaging machines come with several advanced features designed to meet the diverse requirements of different industries:
- Speed: Many machines can operate at high speeds, filling hundreds or thousands of containers per hour, significantly reducing labor costs.
- Precision: Accurate filling minimizes product waste and ensures consistency in product quality.
- Versatility: Machines can often handle various container types and sizes, from bottles to pouches.
- Automation: Automated systems can reduce human labor, enhance safety, and improve overall efficiency.
Industries That Use Liquid Packaging Machines
Liquid packaging machines serve various sectors, including:
- Food and Beverage: Essential for packaging juices, sauces, dairy products, and alcoholic beverages.
- Pharmaceuticals: Used for packaging liquid medications, ointments, and vaccines.
- Chemicals: Ideal for packaging cleaning solutions, oils, and other industrial fluids.
- Cosmetics: Critical for bottling lotions, shampoos, and other liquid products.
Choosing the Right Supplier
What to Look for in a Supplier
Selecting a reputable supplier for liquid packaging machines is vital for ensuring quality and reliability. Here are a few key factors to consider:
- Experience: A supplier with extensive industry experience will likely offer better products tailored to specific needs.
- Technical Support: Look for suppliers that provide comprehensive support, from installation to maintenance.
- Customization: Suppliers should offer machines that can be tailored to meet specific operational requirements.
- Quality Assurance: Ensure the machines meet industry standards and come with warranties or guarantees.
Evaluating Supplier Reputation
Reputation plays a crucial role in selecting a supplier. Research potential suppliers by:
- Reading Reviews: Customer reviews and testimonials can provide insight into a supplier’s reliability and product effectiveness.
- Requesting References: Don’t hesitate to ask for references from past clients to understand their experiences.
- Checking Industry Certifications: Certification from reputable organizations can indicate the supplier’s commitment to quality and safety.
Comparing Pricing and Offerings
Pricing is an essential factor in choosing a supplier, but it shouldn’t be the sole consideration. Evaluate the full range of offerings, including:
- Initial Cost: Compare prices for similar machines, but also consider features and quality.
- Long-Term Value: Assess the machine’s durability, maintenance requirements, and resale value.
- Flexible Financing Options: Some suppliers may offer leasing or financing options that can influence your decision.
Types of Liquid Packaging Machines
Automatic vs. Manual Machines
When investing in liquid packaging solutions, businesses must decide between automatic and manual machines:
- Automatic Machines: These machines typically offer higher efficiency and lower labor costs while requiring less human intervention. They are best suited for high-volume production settings.
- Manual Machines: Ideal for smaller operations or startups where there are lower production volumes. Manual machines may require more labor but are often more affordable.
Popular Machine Types in the Market
Several types of liquid packaging machines are extensively used across industries:
- Filling Machines: Automated systems designed to fill containers with precise quantities of liquid.
- Capping Machines: These secure caps on bottles after filling.
- Labeling Machines: Attach labels to containers with accurate positioning for branding and regulatory compliance.
Innovative Technologies in Liquid Packaging
The liquid packaging industry is continuously evolving with the integration of innovative technologies:
- Smart Technology: Some machines come equipped with sensors and IoT connectivity, allowing for real-time monitoring and data analytics.
- Robotics: Automated robotic systems streamline processes and improve precision, especially in high-speed environments.
- Eco-friendly Solutions: The latest machines are being designed to minimize waste and energy consumption, catering to the growing demand for sustainability.
Best Practices for Operating Liquid Packaging Machines
Maintenance Tips to Ensure Longevity
Proper maintenance is crucial for the longevity and efficiency of liquid packaging machines. Consider these key practices:
- Regular Inspections: Routine checks can identify potential issues before they escalate, ensuring smooth machinery operation.
- Scheduled Maintenance: Following the manufacturer’s guidelines on maintenance schedules can significantly extend machine lifespan.
- Cleaning Protocols: Develop a cleaning routine to keep machines free from contaminants that could affect product quality.
Optimal Settings for Different Products
Each type of liquid product has unique packaging requirements. Here are some considerations:
- Viscosity: Adjust the machine settings based on the liquid’s thickness to avoid spills and enhance filling speed.
- Container Type: Different bottles or pouches may require various settings; ensure the machine settings match the selected container.
- Temperature Control: Some products may need temperature regulation during packaging. Ensure the equipment accommodates such needs.
Employee Training and Safety Measures
Well-trained employees play a vital role in the successful operation of liquid packaging machines. Implement the following:
- Comprehensive Training: Provide detailed training on operating the machinery safely and effectively.
- Safety Protocols: Establish clear safety guidelines to protect employees from potential hazards while operating equipment.
- Frequent Refresher Courses: Regularly update training sessions to reflect any changes in technology or safety practices.
Future of Liquid Packaging Solutions
Trends in the Packaging Industry
The liquid packaging sector is witnessing several noteworthy trends that impact operational strategies:
- Sustainability: There is an increasing emphasis on eco-friendly packaging materials, pushing manufacturers to adapt practices that minimize environmental impact.
- Personalization: Consumers now expect more personalized products; thus, machines must cater to smaller, custom orders without compromising efficiency.
- Smart Technology Integration: The shift towards smart factories is encouraging the adoption of systems that can communicate and adapt autonomously.
Environmental Impact and Sustainability
The packaging industry faces pressure to reduce its carbon footprint. Suppliers are responding by:
- Innovating Packaging Materials: Employing biodegradable materials and recyclable packaging solutions to reduce waste.
- Energy Efficiency: Offering machines designed to consume less energy during operation, minimizing operational costs and carbon emissions.
The Role of Automation in Liquid Packaging
As industries continue to grow, automation within liquid packaging is expected to increase. Benefits include:
- Increased Speed and Accuracy: Automated systems can execute processes much faster while ensuring greater accuracy, reducing human error.
- Labor Cost Reduction: With automation, companies can lower labor costs while reallocating staff to more strategic areas of operation.
- Enhanced Flexibility: Automation allows for rapid reconfiguration of machines to accommodate different products or packaging styles without extensive downtime.